CNC milling aluminum is a common practice in various industries, from aerospace to automotive, due to aluminum’s desirable properties such as lightweight, excellent machinability, and corrosion resistance. However, achieving optimal results in aluminum milling requires a deep understanding of best practices and considerations specific to this material. This article aims to provide insights into the best practices for CNC milling aluminum, along with addressing frequently asked questions (FAQs) to help you enhance your aluminum milling processes.
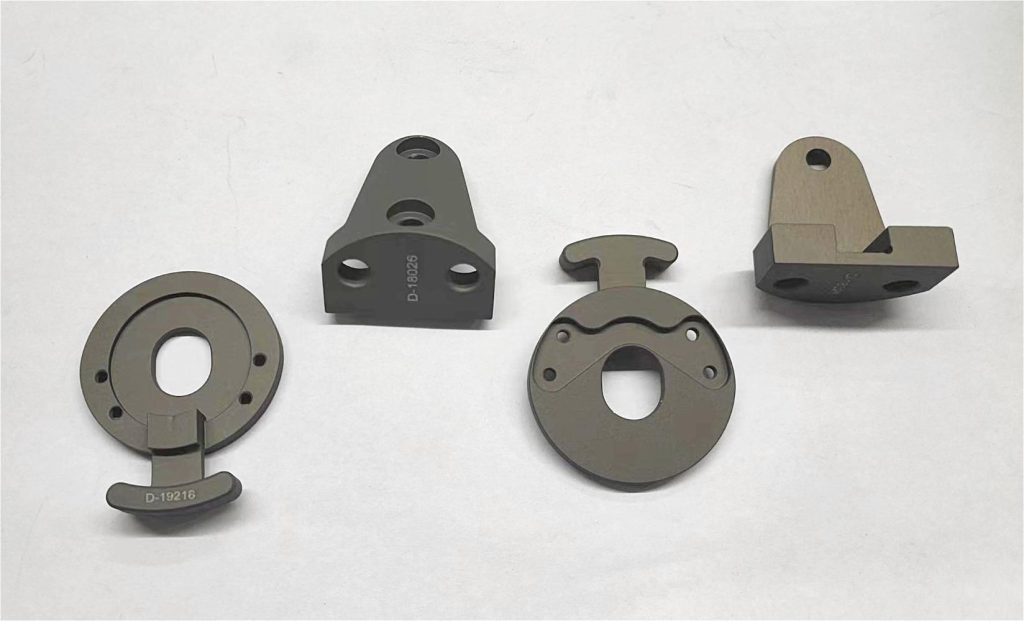
Best Practices for CNC Milling Aluminum
- Material Selection:
- Alloy Selection: Different aluminum alloys have varying strengths, machinability characteristics, and post-processing requirements. Common choices include:
6061: Versatile, good strength-to-weight ratio, ideal for general applications.
5052: Excellent corrosion resistance, good for marine environments.
7075: High strength, used in aerospace and demanding applications (requires specific tooling and techniques).
- Material Thickness: Consider the desired final part thickness and choose appropriate stock material. Thicker materials require more powerful machines and adjusted cutting parameters.
- Tooling Selection:
- Tool Material: High-speed steel (HSS) is generally not recommended due to its softness at high milling speeds. Opt for carbide end mills specifically designed for aluminum machining.
- Number of Flutes: Two-flute end mills are common for good chip evacuation. For finer finishes, three or more flutes can be used.
- Coating: Consider AlTiN (Aluminum Titanium Nitride) coated tools for improved wear resistance and chip evacuation.
- Machining Parameters:
Optimizing machining parameters such as spindle speed, feed rate, and thickness of cut is critical for achieving high productivity and surface finish while minimizing tool wear. Key guidelines include:
- Cutting Speeds and Feeds: Aluminum benefits from high cutting speeds (up to 10,000 RPM or more) and moderate feed rates. Utilize a feeds and speeds calculator or refer to manufacturer recommendations for specific tools and aluminum alloys.
- Chip Thickness: Maintain a chip thickness of 0.1mm to 0.3mm per tooth for optimal performance and tool life.
- Step-Over and Step-Down: Use shallow step-over (engagement with the material) of 0.05mm to 0.1mm and adjust step-down (depth per cut) based on tool diameter and desired finish.
- Coolant and Lubrication:
While aluminum has excellent thermal conductivity, using coolant or lubricant during milling can help dissipate heat and improve chip evacuation. However, some operations can be performed dry, especially with the right tooling and machining parameters, reducing the need for coolant and minimizing cleanup efforts.
- Flood Cooling: When possible, utilize a flood coolant system to effectively dissipate heat, improve chip evacuation, and extend tool life. A water-soluble coolant with a lubricant additive is recommended for aluminum.
- Minimum Quantity Lubrication (MQL): For certain applications, a mist coolant or MQL system can be used to minimize coolant usage and environmental impact.
- Workholding:
Securely holding aluminum workpieces during milling is essential to prevent vibration and ensure accuracy. Common workholding solutions include:
- Vacuum Chucks: Ideal for flat or thin workpieces, vacuum chucks provide stability and accessibility to all surfaces.
- Clamps and Fixtures: Utilize clamps and fixtures designed specifically for aluminum machining to provide secure and stable workpiece support.
- Programming and Toolpath Generation:
Utilize CAM software to generate efficient toolpaths, considering factors such as:
- Tool Engagement: Minimize tool deflection and vibration by optimizing tool engagement and cutting conditions.
- Cutting Direction: Consider the direction of cuts to minimize tool wear and maximize chip evacuation.
- Adaptive Machining: Employ adaptive machining strategies to maximize material removal rates and surface quality while minimizing tool wear.
By adhering to these best practices, manufacturers can optimize their CNC milling processes for aluminum, resulting in high-quality parts with excellent dimensional accuracy and surface finish.
FAQs about CNC Milling Aluminum
Q1. What is the best tool for milling aluminum?
There isn’t a single “best” tool. The optimal choice depends on factors like the specific aluminum alloy, desired surface finish, and machining operation (roughing or finishing). Generally, carbide end mills with two or more flutes and AlTiN coating are well-suited for aluminum milling.
Carbide end mills with high helix angles and sharp edges are preferred for aluminum milling due to their excellent chip evacuation capabilities and heat resistance.
Q2. Can I mill aluminum dry?
Technically yes, but it’s not recommended. Dry milling generates excessive heat, leading to rapid tool wear, poor surface finish, and potential workpiece warping. Using a coolant or lubricant significantly improves the machining process.
Q3. How can I prevent aluminum from sticking to cutting tools?
- Utilize proper coolant and lubrication.
- Maintain sharp cutting edges.
- Optimize chip evacuation with appropriate tool selection and chip breaker geometries. Cutting tools with coatings such as TiCN or TiAlN is ok.
- Reduce cutting forces by adjusting feed rates and step-over values.
Q4: How can I improve surface finish when milling aluminum?
- Use sharp cutting tools: Dull tools can cause rough surfaces. Ensure your cutting tools are sharp and in good condition.
- Optimize toolpath: Consider using climb milling instead of conventional milling as it tends to produce a better surface finish.
- Use proper coolant/lubrication: Appropriate coolant/lubrication can help reduce heat and friction, resulting in smoother surface finishes.
- Control chip evacuation: Proper chip evacuation prevents recutting of chips, which can mar the surface finish.
- Consider reducing feed rates: Lower feed rates can sometimes improve surface finish, especially when using high-speed machining techniques.
Q5: What are the typical speeds and feeds for aluminum milling?
Typical speeds and feeds for aluminum milling depend on several factors including the type of aluminum alloy, cutter geometry, machine rigidity, and desired surface finish. However, as a general guideline, for aluminum milling using carbide end mills, typical speeds and feeds range as follows:
- Speeds: Typical cutting speeds for aluminum range from 500 to 3000 surface feet per minute (SFM). Higher speeds are often used for softer aluminum alloys.
- Feeds: Feed rates depend on various factors including tool diameter, material hardness, and machine rigidity. Generally, feed rates range from 0.002 to 0.010 inches per tooth.
Q6: What factors affect the cost of CNC milling aluminum?
Several factors affect the cost of CNC milling aluminum, including material cost, machine time, tooling costs, complexity of the part geometry, tolerances required, surface finish specifications, and any additional finishing processes such as anodizing or painting. Optimization of toolpaths and machining strategies can also impact cost by reducing machining time and tool wear.
Conclusion
CNC milling aluminum can yield high-quality parts with excellent dimensional accuracy and surface finish when proper techniques and best practices are employed. By carefully selecting materials, tools, machining parameters, and addressing common challenges through effective chip evacuation and surface finish improvement strategies, manufacturers can optimize their aluminum milling processes for increased efficiency and cost-effectiveness.