The world of CNC machining opens up a world of possibilities for creating custom parts and components. From complex aerospace components to sleek phone cases, the versatility of this technology is dependent on one critical factor: material selection. Choosing the right material can help take your project from functional to phenomenal. This comprehensive guide delves into the key factors influencing material selection for CNC machining, allowing you to make more informed decisions for your next project. We’ll look at various material options, from classic metals to modern plastics, highlighting their distinct properties and applications.
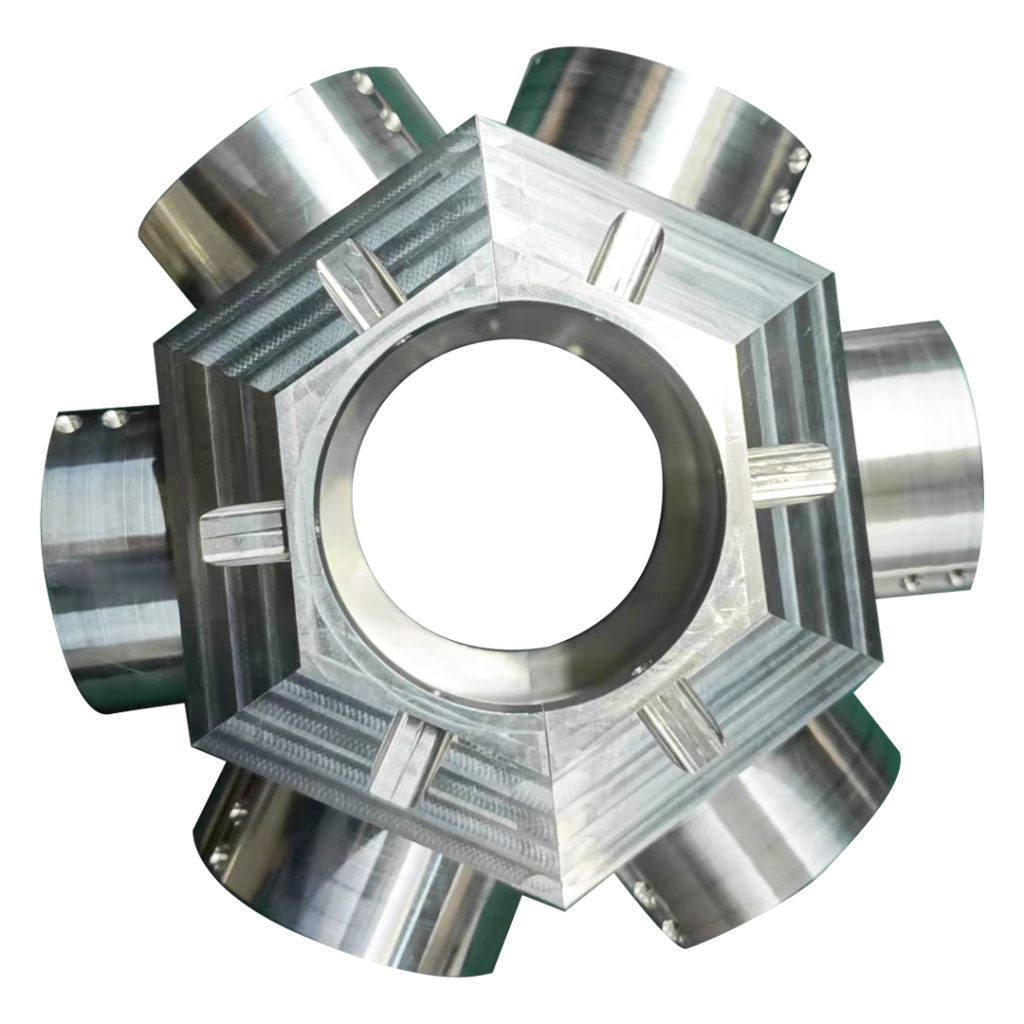
Factors That Affect The Choice of CNC Machining Materials
Selecting the right material for your CNC machining project is crucial for functionality, cost, and overall success. Here’s a detailed breakdown of the key factors influencing material choice:
Factor 1: Part application
- Functionality: The material chosen for the part is directly influenced by its intended use. For example, a lightweight component for an airplane requires a different material than heavy-duty equipment for a construction machine. The part application specifies the required strength, weight, heat resistance, electrical conductivity, and other critical properties.
- Material Properties Dictate Performance: Different materials have unique strengths and weaknesses. Understanding the part’s application allows you to choose a material with properties that ensure it performs its intended function effectively. For example, a door hinge requires a strong and durable material such as steel, whereas a decorative lampshade may prefer a lightweight and aesthetically pleasing material such as aluminum.
- Optimizing Design and Cost: Choosing the right material for the application optimizes both functionality and cost-effectiveness. For example, using an overly strong material for a non-load-bearing component adds unnecessary weight and cost. In contrast, using a weak material in a high-stress application may result in part failure and potential safety hazards.
Factor 2: Dimensional Stability and Tolerance
- CNC machining relies on precise control: The entire process revolves around precisely removing material according to a digital design. The machine expects the material to behave predictably throughout the process.
- Material properties can affect final dimensions: Some materials exhibit greater shrinkage, warping, or expansion during machining due to internal stresses, heat, or moisture absorption. These changes may cause the part’s final dimensions to be incorrect.
- Tolerance defines acceptable variation: Even the most precise CNC machines cannot achieve absolute perfection. Tolerances define an acceptable range of variation in a part’s dimensions.
Factor 3: Machinability
- Production Time and Cost: Materials with high machinability are easier to cut, requiring less machining time and tool changes. This results in faster production and lower total costs. In contrast, difficult-to-machine materials take longer to process, resulting in increased machining time, increased tool wear, and the potential need for specialized tools, all of which raise production costs.
- Surface Finish: Machinability helps you achieve the desired surface finish on your part. Materials that machine well produce smoother finishes and require fewer post-processing steps, such as polishing. Difficult-to-machine materials may result in a rougher surface finish, necessitating additional work to achieve the desired smoothness, increasing production time and cost.
- Tool Life and Maintenance: Highly machinable materials are gentler on cutting tools, increasing their lifespan. This reduces the need for frequent tool changes and maintenance downtime. Hard-to-machine materials, on the other hand, wear down cutting tools more quickly, requiring more frequent replacements and increasing maintenance costs.
- Process Feasibility: Some extremely hard or brittle materials may be difficult or impossible to machine using standard CNC techniques. Poor machinability can make it difficult to achieve desirable design features or tolerances. In such cases, alternative materials with higher machinability may be required, as well as specialized machining techniques, which can increase complexity and costs.
Factor 4: Physical Appearance
- Aesthetics: In many applications, particularly consumer products, the final appearance and feel of the machined part are critical. For example, a phone case or watch band may require a specific color, texture, or finish to be visually appealing to customers.
- Functionality tied to Appearance: Sometimes appearance serves a functional purpose. A smooth, polished surface may be required for a medical instrument to facilitate cleaning and sterilization. Alternatively, a non-slip grip on a tool handle may necessitate a particular material texture.
- Design Intent: Material selection can be influenced by the overall project design intent. An architect specifying materials for building components may prioritize a sleek, modern aesthetic, resulting in materials such as brushed aluminum or colored plastics.
What Are the Different Material Options for a CNC Machining Project?
The material used for a CNC machining project is determined by several factors, including the project’s intended use, the material’s strength and durability, and cost. Here’s a table of some of the most popular materials used in CNC machining, along with their properties and applications:
Material | Properties | Applications |
Aluminum | Lightweight, strong, and durable;good corrosion resistance | Aerospace,automotive,electronics,medical |
Brass | Easy to machine;good corrosion resistance | Plumbing,electrical,musical instruments |
Copper | Excellent electrical conductivity;good thermal conductivity | Electrical,plumbing,heat sinks |
Steel | Strong and durable;good wear resistance | Automotive,construction,machinery |
Stainless steel | Corrosion-resistant;strong and durable | Medical,food processing,chemical processing |
Plastic | Lightweight;variety of colors and finishes available | Automotive,electronics,consumer goods |
Wood | Natural, renewable resources;easy to machine | Furniture,cabinetry,toys |
Frequently Asked Questions
Here are the answers to some commonly asked questions regarding choosing the best material for a CNC manufacturing process:
Q1: What Is the Most Commonly Used Material for CNC Machining?
A1: Steel, aluminum, and plastic are common materials used in CNC manufacturing. Aluminum is the most popular choice. It’s lightweight but strong, corrosion-resistant, and an excellent heat and electricity conductor. This makes it suitable for a wide range of applications across multiple industries. Aluminum is easier to machine than steel, which leads to faster production times and lower machining costs. Aluminum strikes a good balance between price and performance, making it a popular choice for many projects.
Q2: What Are the Difficult Materials to CNC Machine?
A2: Heat-treated alloys, such as alloy steel and cobalt-based alloys, are typically the most difficult to machine. These materials cause excessive wear on cutting tools. Specialized and expensive tools such as diamond-coated cutters may be required, raising production costs. Slower machining speeds are frequently required to avoid tool breakage and ensure chip formation, which adds to production time. Some hardened alloys are brittle and can fracture under high machining stress. To prevent damage to the workpiece, careful toolpath planning and parameter adjustments are required.
Q3: Which CNC Machining Material Has the Highest Machinability?
A3: Free-machining steel has the highest machinability. Plastics and composites are easier to cut, but they can react negatively to high temperatures produced during the cutting process. Free-machining steels contain additives such as sulfur or lead, which encourage the formation of short, broken chips while machining. This reduces tool wear and improves the surface finish. The additives also act as lubricants during the cutting process, reducing friction and heat generation and increasing tool life. These steel’s machinability ratings are based on a standard reference material (usually B1112 aluminum). Ratings greater than 100% indicate better machinability than the reference material, with some free-machining steels reaching ratings of up to 300%.
Q4: Which Is the Best Material For a CNC Machining Project?
A4: No single material can be considered ideal for all CNC machining projects. Different materials have distinct properties and purposes, but aluminum is the most widely used due to its flexibility and suitability for the majority of applications.
Conclusion
Remember that the ideal material selection is dependent on careful consideration of your project’s specific requirements. Prioritize factors such as strength, weight, machinability, and aesthetics to determine the best material for your design. Do not hesitate to seek expert advice from CNC machining professionals. With the knowledge gained from this guide and the assistance of experienced machinists, you’ll be well on your way to turning your vision into a tangible reality using the power of CNC manufacturing. JTR also provides professional cnc machining services. If you need it, please contact us.