Anodizing is an electrochemical process used to strengthen and protect the surface of aluminum. It essentially involves thickening the metal’s naturally occurring oxide layer to achieve a long-lasting, corrosion-resistant, and decorative finish. Anodizing significantly improves aluminum’s surface hardness and wear resistance, making it suitable for demanding applications. The oxide layer acts as a barrier, protecting the underlying aluminum from rust and other types of corrosion. Anodized coatings typically last 10 to 20 years, but several factors can affect their longevity. This article gives a brief overview and tips for extending the life of anodized coatings.
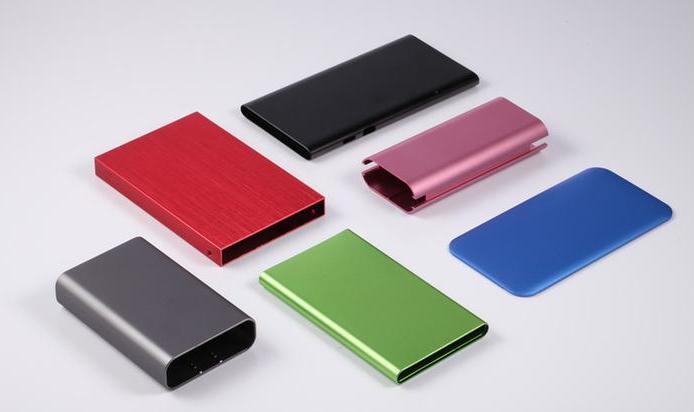
What Factors Can Affect the Lifespan of an Anodized Coating?
Factor | Description | Impact on Lifespan |
Thickness | Refers to the microscopic layer of oxide created during anodizing. | Thicker coatings generally offer longer lifespans due to increased protection against wear and tear. |
Type of Anodizing | Different anodizing processes create coatings with varying properties. | Hard anodizing typically offers a superior lifespan compared to conventional anodizing due to its denser and harder layer. |
Post-Treatment Sealing | A process that closes the microscopic pores in the anodized layer. | Sealing improves corrosion resistance and extends lifespan by preventing the penetration of moisture and contaminants. |
Environment | The surrounding conditions where the anodized object is used. | Harsh environments like exposure to UV rays, salt, extreme temperatures, or strong chemicals can accelerate wear and shorten lifespan. |
How Does the Type of Metal Being Anodized Affect the Lifespan of the Coating?
Metal | Anodizing Process | Typical Coating Thickness | Characteristics | Lifespan |
Aluminum | Sulfuric acid anodizing | 0.001-0.002 inches | Excellent corrosion resistance, good wear resistance, variety of colors available | 10-20 years |
Titanium | Chromic acid anodizing | 0.0005-0.001 inches | Superior corrosion resistance, good biocompatibility, high strength | 20-30 years |
Magnesium | Chromic acid anodizing | 0.0005-0.001 inches | Good corrosion resistance, lightweight, low cost | 5-10 years |
Steel | Sulfuric acid or chromic acid anodizing | 0.0005-0.002 inches | Improved corrosion resistance, increased wear resistance, paintable | 10-20 years |
How Does the Intended Use of the Anodized Object Impact the Expected Lifespan of the Coating?
Intended Use | Environment | Expected Lifespan Impact |
Indoor | Protected from harsh elements (UV rays, rain, extreme temperatures) | Longer lifespan due to minimal exposure to degrading factors. |
Outdoor | Exposed to sunlight, rain, wind, and temperature fluctuations | Shorter lifespan compared to indoor use due to constant weathering and potential for scratches or abrasions. |
Marine (e.g., boats, fishing equipment) | Exposed to salt water, UV rays, and harsh weather conditions | Shortest lifespan due to the highly corrosive nature of salt water and the combined effects of other environmental factors. |
High-wear applications (e.g., machine parts, tools) | Subject to frequent friction, scratches, and potential impacts | Potentially shorter lifespan depending on the severity and frequency of wear. Regular maintenance and touch-ups might be necessary. |
Tips to Extend the Lifespan of Anodized Coatings:
It is important to know how to care for anodized coatings.JTR once published an article about how to care for anodized aluminum, If you are interested in it you can read it. There are a lot of complex knowledge and skills that need to be understood. And there is a list of some tips to extend the lifespan of anodized coatings.
Proper cleaning
To clean anodized surfaces, use mild soap and water or specialized cleaning products. Avoid using harsh chemicals or abrasive sponges. Dirt, dust, and other debris can act as abrasives on the surface, leaving microscopic scratches over time. These scratches weaken the coating, increasing its susceptibility to future damage and wear. The anodized layer serves as a barrier, protecting the underlying metal. Proper cleaning keeps this layer clean and intact, increasing its effectiveness and extending the overall life of the coating.
Regular maintenance
Inspect the anodized surface on a regular basis for signs of wear and damage. Regular inspections allow for the early detection of potential issues like scratches, chips, and fading. By detecting minor issues early on, you can take preventive measures like touch-ups or extra protective coatings to limit further damage and ensure the anodized layer’s longevity.
Minimize exposure to harsh environments
When possible, avoid exposure to direct sunlight, salt water, extreme temperatures, and harsh chemicals. Direct sunlight can wear down the anodized layer over time. UV radiation degrades the oxide layer, causing fading, chalking, and loss of gloss. This reduces the coating’s protective properties. Harsh environments, such as saltwater, acidic rain, and high humidity, can accelerate corrosion. These elements degrade both the anodized layer and the underlying metal, causing surface deterioration and jeopardizing the coating’s integrity. Extremely high or low temperatures can cause the anodized layer to crack. This increases the likelihood of chipping, peeling, and eventual failure.
Conclusion
Anodizing is a durable and versatile surface treatment that can be used for a variety of applications. While the typical lifespan ranges from 10 to 20 years, understanding the factors that influence its longevity, such as coating thickness, sealing quality, metal type, and intended use, allows for more informed decisions. Following the advice above will help you extend the life of your anodized products while also preserving their beauty and functionality. Remember that proper care and maintenance are critical to extending the life of any surface treatment, including anodizing. JTR provides professional anodizing service, if you need this service please choose us.