CNC machining, also known as computer numerically controlled machining, is a precise manufacturing process that forms aluminum into intricate and complex parts using computer-programmed tools. This process has a lot going for it when it comes to aluminum because it cuts the tough but soft metal very well, producing parts with excellent durability, excellent strength-to-weight ratios, and high dimensional accuracy. Through the process of CNC machining, aluminum can be fully utilized for a wide range of applications, including precision-machined medical instruments, automotive parts that require strength, and aircraft parts that must be lightweight. Aluminum is a material that is valuable to many industries. There are some important design considerations for CNC machining aluminum parts:
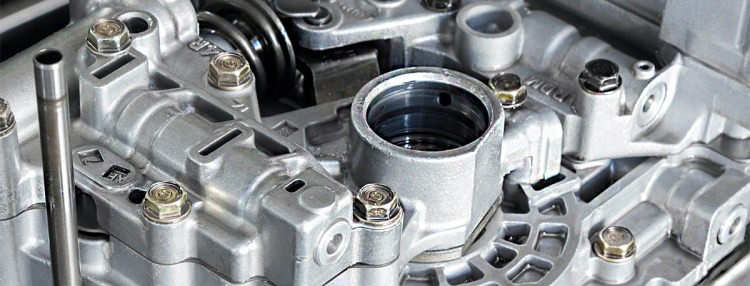
Consideration 1: Wall Thickness
Maintaining the proper wall thickness is essential for strength and stability because aluminum is a relatively thin material that is prone to warping. Wall thickness plays a crucial role in CNC machining aluminum parts for several key reasons:
- Strength and Stability: Aluminum can bend and warp under stress, especially when it’s thin, despite being strong for its weight. It is ensured that the part can withstand the intended load and machining forces without deforming by maintaining the proper wall thickness throughout.
- Tool Reach and Accessibility: CNC tools may have trouble reaching and maneuvering through thin walls. With limited clearance, some internal cavities or features may become inaccessible. This can result in incomplete machining or the need for specialized, smaller tools, which can be expensive and ineffective.
- Chip Accumulation and Heat Dissipation: Aluminum shavings, or chips, build up around the cutting tool during machining. Thin walls reduce the amount of space available for chip evacuation, which increases the risk of clogging and overheating. This may result in part failure, machining accuracy issues, and tool damage. Furthermore, thin walls have a reduced ability to dissipate heat produced during machining, which raises the possibility of part distortion and tool wear.
- Cost and Material Efficiency: More material is needed for thicker walls by nature, but building walls that are too thick also wastes resources and raises production costs. For cost-effective CNC machining, the ideal balance between adequate strength and effective material usage must be found.
- Maintaining Design Intent: Overly thin walls may compromise the design intent and necessitate redesign or alternative manufacturing techniques to accommodate essential features like threaded holes or intricate details.
Consideration 2: Features and Tolerances
Design elements that affect cost and viability include undercuts, sharp corners, and tight tolerances, which may call for specialized tools or processes. Why are tolerances and features so important? Let’s delve into the reasons:
- Machinability: Aluminum has peculiarities despite its versatility. The CNC tools may have difficulty navigating intricate details, thin walls, and sharp corners. Creating features that are simple to machine not only speeds up production but also lowers tool wear and tear, which saves money.
- Precision Matters: Even though CNC machines are precision experts, they have their limitations. Miniscule permitted variations in dimensions, or tight tolerances, can be difficult to attain and greatly raise production costs.
- Think Assembly: When designing an aluminum part that must work well with others, assembly features must be taken into account. An easy and effective assembly process is ensured by design elements like threaded holes, slots, and interlocking tabs that blend in seamlessly with other parts.
Consideration 3: Draft Angles
Tiny draft angles on vertical features facilitate part removal from the mold and help to keep it from jamming. Draft angles are crucial for CNC machining aluminum parts for several reasons:
- Part Removal: Vertical walls or cavities are a common feature of aluminum parts. In the absence of draft angles, these characteristics would function as hooks, tightly grasping the mold and making it challenging, if not impossible, to remove the completed part without breaking it or the mold.
- Reduced Risk of Damage: The force exerted upon extracting a part devoid of draft angles may result in rips, rips, or distortions. This can jeopardize the part’s dimensional accuracy and is especially harmful to surface finishes. Draft angles ensure the part maintains its intended form and finish by reducing friction and the resulting damage risk.
- Tool Wear and Efficiency: Attempting to extract a jammed part can significantly strain the machining instruments. This quickens the deterioration of tools, raising production costs overall and possibly necessitating tool replacements. By making part removal easier, lessening the strain on the tools, and increasing their lifespan, draft angles help avoid such situations.
- Cost-Effectiveness: The budget and deadlines can be greatly affected by production delays resulting from problems with part removal and frequent tool replacements.
Consideration 4: Material Selection
Based on the required levels of corrosion resistance, machinability, and desired mechanical properties, select the appropriate aluminum alloy. Material selection is crucial for CNC machining aluminum parts for several reasons:
- Impact on Machinability: The ease of cutting, chip formation, and tool wear of various aluminum alloys vary. Selecting the appropriate alloy reduces tool wear and guarantees a smooth, efficient machining process, all of which have an impact on production costs and schedule.
- Desired Mechanical Properties: Specific strength, stiffness, weight, and ductility are required for the finished part. These qualities can be found in varying combinations in different alloys. Selecting the incorrect alloy could result in parts that are too heavy, too brittle, or too ductile for the intended use.
- Corrosion Resistance: Corrosion resistance may be crucial, depending on the environment in which the part is intended to be utilized. Certain aluminum alloys are more naturally resistant to corrosion than others. Selecting the appropriate alloy guarantees that the part won’t break down over time, particularly in challenging conditions.
- Cost and Availability: A variety of alloys differ in price and accessibility. Although certain high-performance alloys have better qualities, their costs may be much higher or their lead times may be longer.
- Design Flexibility: Some alloys are more suited for intricate features and complex geometries because of their ductility and machinability.
Conclusion
When CNC machining aluminum parts, design factors are crucial because they impact the part’s machinability, the precision of the machining process, and the production cost. Designers can make sure that their parts are affordable to produce, easy to machine, and meet the necessary specifications by carefully taking these factors into account. Rapid prototyping, precision parts, tooling machining, and end-use parts are just a few of the CNC machining parts that JTR can provide for you as one of the top suppliers of precision CNC machining services in China.